一、技术架构革新
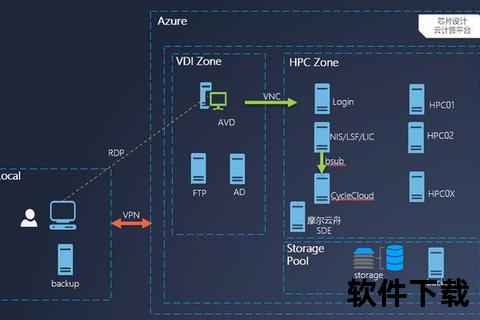
随着算力提升与算法优化,新一代CAD系统通过异构计算架构实现了百倍级性能跃升。达索系统推出的3DEXPERIENCE平台采用分布式计算技术,使复杂装配体仿真时间从数小时缩短至分钟级。这种底层技术突破不仅改变了传统串行设计流程,更使得实时渲染、多物理场耦合分析成为可能。
参数化引擎的智能化重构是另一项关键技术突破。Autodesk研发的衍生式设计模块,通过机器学习算法将设计约束转化为数学拓扑结构。工程师只需输入功能需求与边界条件,系统即可生成数百种优化方案。波音公司应用该技术开发787机翼结构,成功实现减重15%的同时提升结构强度,验证了智能算法的工程价值。
二、工程流程再造
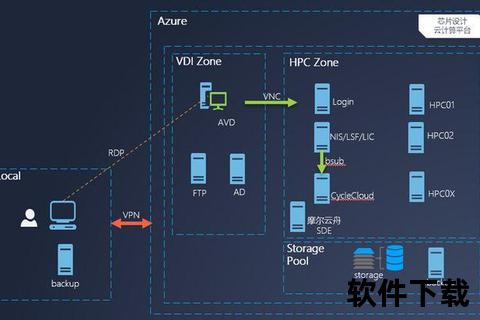
高效能CAD推动设计流程从线性迭代向并行协同转变。西门子NX软件构建的数字化主线技术,将概念设计、仿真验证、工艺规划等环节整合在统一数据平台。据麦肯锡研究报告显示,这种集成化工作流使汽车研发周期缩短40%,变更响应速度提升60%。工程师可以实时查看设计修改对制造可行性的影响,从根本上改变传统"设计-验证-返工"的循环模式。
基于云原生的协同设计正在重塑全球工程网络。PTC的Onshape平台支持200人实时协同操作三维模型,版本控制精度达到0.01秒级。在港珠澳大桥项目中,中外设计团队通过云端协作完成12万张图纸同步更新,避免了传统文件传输导致的数据滞后问题。这种突破物理边界的协作模式,使跨时区工程协同效率提升300%。
三、智能设计跃升
生成式AI与CAD的深度融合开创了设计新范式。ANSYS Discovery将物理仿真引擎嵌入建模环境,实现"设计即仿真"的颠覆性体验。工程师拖动模型参数时,应力云图、流体轨迹实时动态更新。宝马集团应用该技术开发电动车底盘,将悬架系统优化周期从3个月压缩至72小时,设计迭代次数减少85%。
知识图谱技术正在构建工程智慧大脑。达索系统的CATIA知识工程模块,将企业历史设计数据转化为可复用的设计规则库。空客A350项目通过继承200万条设计规则,新机型研发节省了120万工程师小时。这种知识沉淀机制使设计经验不再是离散的个体记忆,而是可量化传承的组织资产。
四、生态体系重构
版权声明:如无特殊标注,文章均为本站原创,转载时请以链接形式注明文章出处。