一、实时监测与预警革新
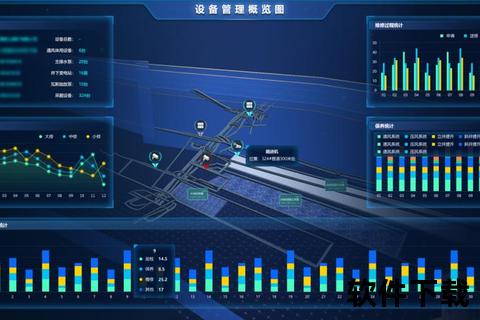
在工业设备管理领域,智能诊断AI软件通过高频数据采集系统实现了毫秒级状态监控。传感器网络实时传输振动、温度、电流等关键参数至云端分析平台,相较于传统人工巡检的周检或月检频率,监测密度提升逾百倍。美国通用电气公司2023年报告显示,其Predix平台用户设备故障误报率降低62%,得益于AI算法对噪声信号的有效过滤。
深度神经网络构建的多维特征模型,能够识别设备劣化的早期征兆。例如,某风电企业通过分析齿轮箱振动频谱中的次谐波分量,将轴承故障预警时间从72小时提前至240小时。这种预测能力的突破,使得维护团队可从容调度备件资源,避免因紧急抢修造成的生产中断。日本三菱重工的实际案例表明,AI预警系统使涡轮机组的非计划停机时长缩短41%。
二、决策模型优化升级
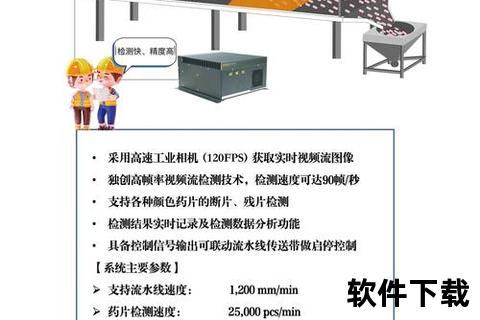
基于设备全生命周期数据的知识图谱,AI系统可生成动态维护策略库。德国博世工厂的实践显示,算法在分析15万台设备历史数据后,将润滑周期从固定2000小时调整为1200-2800小时的弹性区间,关键部件寿命延长18%。这种自适应调整能力,突破了传统维护规程的刚性约束。
蒙特卡洛树搜索算法的引入,实现了多目标优化决策。当面对设备可靠性、维护成本和生产计划的三重约束时,AI系统可在0.3秒内生成帕累托最优解集。中国宝钢集团的应用数据显示,该方法使年度维护预算节省2300万元,同时关键设备可用率提升2.7个百分点。这种决策效率的提升,彻底改变了依赖工程师经验的传统决策模式。
三、知识沉淀与传承突破
自然语言处理技术构建的故障案例库,解决了企业知识流失难题。通过解析30年维保记录,AI系统提炼出127种典型故障的处置范式,形成可检索的结构化知识体系。韩国三星电子实施该系统后,新入职工程师的故障诊断准确率在3个月内从58%提升至89%,显著缩短人才培养周期。
联邦学习框架的部署,实现了跨厂区知识的安全共享。某跨国汽车集团通过加密参数交换,使中国工厂能即时获取德国母工厂的设备维护经验,成功将冲压模具的异常检测准确率提升33%。这种知识协同效应,打破了传统单点作战的局限,构建起全球化的设备健康管理网络。
四、经济效益多维提升
全要素成本分析模型揭示,AI系统带来的价值远超硬件投入。荷兰皇家壳牌集团的测算表明,每投入1美元在智能诊断系统,可获得4.3美元的综合收益,涵盖能耗降低、产能提升和保险费用下降等多个维度。特别是对高价值设备而言,寿命延长1%就意味着数百万美元的资产保值。
供应链层面的涟漪效应正在显现。当核心企业采用AI维护系统后,上下游供应商的协同响应速度提升60%。丰田汽车供应商的实践显示,基于预测性维护数据的精准要货,使库存周转率提高1.8倍。这种产业链级别的效率提升,正在重塑现代制造业的竞争格局。
随着数字孪生技术与5G网络的深度融合,设备健康管理正迈向虚实交互的新纪元。英国罗尔斯罗伊斯公司开发的航空发动机数字镜像,已能模拟3000种工况下的性能衰减路径。未来,量子计算有望将复杂系统的故障预测精度提升至分子级别。这场由智能诊断AI引领的维护革命,不仅持续释放设备潜能,更在重构工业企业的核心竞争力版图。当维护活动从成本中心转型为价值创造引擎,制造业的可持续发展之路将越走越宽广。